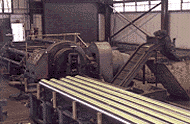 |
Empezamos en el área de recepción
de materiales primas donde se reciben barras de diversa composición
química. Las barras inoxidables son maquinadas de ser necesario
al diámetro requerido por la prensa de extrusión de
5.500", 6.850", 7.500", 8.080", o 9.000"
con un pelador de barras Medart. La razón de maquinar el
diámetro exterior es para remover las imperfecciones del
laminador en caliente, asegurando así una terminación
superficial satisfactoria después de la extrusión.
Después del pelador de barras,
el material se manda a uno de cuatro serruchos para cortar al largo
requerido para extrusión. Palanquilla se refiere a barras
cortas. Las palanquillas se cortan para lograr el largo optimo final
del producto para minimizar la perdida metálica. Las palanquillas
tienen un radio maquinado en el ángulo exterior, para estimular
el flujo inicial de metal, y se limpia para sacar el aceite del
maquinado.
|
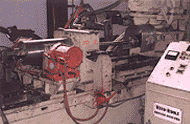 |
Los números de
proceso se imprime en cada palanquilla individual para asegurar control
absoluto de identidad de las piezas. Las palanquillas se mueven al
interior de un horno rotativo a gas de 10 toneladas por hora. Si el
producto que se produce es tubular o una pieza con un agujero, luego
la palanquilla se transfiere a una prensa perforadora de 650 toneladas
que hace un agujero en el centro de la palanquilla, sin embargo, |
|
productos con un diámetro
interior final de 2.187" o menos se perforan a la misma medida
que el mandril, evitando así la prensa perforadora, tal como
se hace con las piezas sólidas. |
Sea sólido
o tubular, la palanquilla se trae a la temperatura de extrusión
final con un calentador de inducción. Después del ultimo
recalentamiento, la palanquilla se cubre con vidrio en el diámetro
interior. La palanquilla ahora se pone en la prensa de extrusión.
Un pistón hidráulica empuja la palanquilla adentro de
la cámara, y luego el pistón principal fuerza el material
afuera de la cámara a través de un matriz para formar
el perfil requerido. Se tarda aproximadamente tres segundos para convertir
la palanquilla a una forma extruída. |
Después de extruir la pieza,
se va a requerir terminación que incluye enderezar, desenroscar,
limpiar con arenado y/o decapado, cortar a un largo determinado,
inspeccionar, empaquetar y prepararlo para enviar al cliente.
|
Nuestro
estirador/enderezador de 500 toneladas es unas de las mas grandes
en la industria. La prensa de extrusión de 2500 toneladas y
el estirador/enderezador grande, permite a Amerex producir espesores
mas grandes de secciones de productos y materiales con mas resistencia
que la mayoría de nuestros competidores. Del principio hasta
el final, nos hemos movido hacia eficiencia en producción.
La capacidad de Amerex para diseñar y fabricar matrices de
extrusión permite a Amerex a producir productos extruídos
dentro de 4-6 semanas después que el diseño final tubular
o de piezas es aprobado por el cliente, dependiendo de la programación
de producción en el momento de la orden. Amerex mantiene un
inventario de aceros carbono y grados inoxidables de aleaciones que
permite una repuesta rápida. |
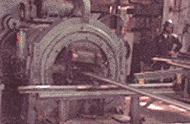
|
|