|
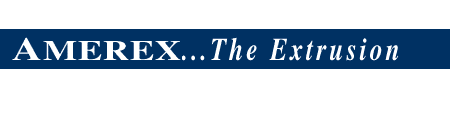 |
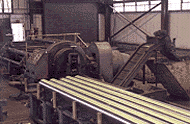 |
We
begin at the raw material receiving area where bars of various
chemistries are received. The stainless bars are machined
to the required extrusion press diameter of 5.500", 6.850",
7.500", 8.080" or 9.000" by a Medart bar peeler,
if required. The reason for machining the OD is to remove
hot rolled imperfections, thus assuring a satisfactory surface
finish after extrusion.
After
the bar peeler, the material is sent to one of four saws to
be cut to the required extrusion length. These short lengths
are referred to as billets. Billets are cut to achieve the
optimum finished length of product to minimize yield loss.
Billets have a radius machined on the outside corner, to promote
initial metal flow, and is cleaned of machining oil.
|
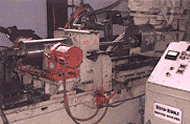 |
Heat
numbers are stamped onto each individual billet to insure
absolute heat number identity control. The billets are then
moved to the entry hearth of a 10 ton per hour gas-fired rotary
furnace. If the product being produced is a tubular product
or a shape with a hole, then the billet is transferred to
a 650 ton peircing press which puts a hole in the middle of
the billet, however, product with a finished ID of 2.187"
or less are drilled to the same size as the mandrel, thus
bypassing the piercing press, as do the solid shapes.
|
|
.
|
|
Whether
solid or tubular, the billet is brought to the final extrusion
temperature by induction heaters. After final heating, the billet
is coated with the glass both on the OD and in the case of tubulars,
on the ID. |
The
billet is then fed into the extrusion press. A hydraulic ram
pushes the billet into the container, after which the main ram
forces the material out of the container through a die to form
the required shape. It takes approximately three seconds to
change the billet into an extruded shape |
After
extruding the shape, it will require finishing which includes
straightening, de-twisting, cleaning by either shot blasting
and/or pickling, cutting to length, inspecting, packaging and
getting ready for shipment to the customer. |
Our 500 ton stretch straightener is one of the largest in the
industry. The 2500 ton extrusion press and large stretch straightener,
allows Amerex to produce larger product section thicknesses
and higher strength materials than most of our competitors.
From start to finish, we have moved toward efficiency in production.
Amerex's die design and die making capabilities permits Amerex
to produce dies and extrude products within four to six weeks
after the final tubular or shape design is approved by the customer,
dependant upon production scheduling at the time of order. Amerex
maintains an inventory of carbon and stainless grades of billets
for quick response. |
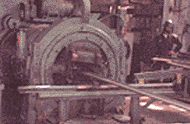
|
|
|
|